Painting Standard AS/NZS 2311 Guide to the Painting of Buildings
At Fresh Coats Painting, we take pride in delivering high-quality finishes that meet industry standards. But what defines a good paint job? Understanding painting inspection guidelines ensures that both homeowners and professionals can fairly assess workmanship. Below, we break down the AS/NZS 2311 Guide to the Painting of Buildings, helping you understand what to expect when evaluating a painted surface.
Assessing Painting Standards and Surface Defects
Determining whether a painted surface meets quality standards can be subjective. To ensure consistency when assessing paintwork, industry guidelines provide clear inspection parameters. These guidelines take into account viewing distances, lighting conditions, and acceptable tolerances, ensuring a fair and standardized approach to evaluating finishes.
Inspection Guidelines for Painted Surfaces
The quality of a painted surface can be affected by several factors, including:
Viewing distance – How far the observer is from the surface
Lighting conditions – Whether the light is natural or artificial, direct or diffused
Angle of observation – The direction and intensity of light hitting the surface
To ensure a fair assessment, paintwork should be viewed from a standard distance under non-critical lighting conditions.
Industry-Standard Viewing Distances
The Guide to Tolerances, Materials, and Workmanship in New Residential Construction (2015), along with painting industry standards such as AS/NZS 2311, establishes the appropriate viewing distances for assessing finishes:
Walls and ceilings: Assessed from 2 meters or more
Fixtures and fittings: Assessed from 600 mm or more
Bathroom and kitchen cabinetry: Assessed from 600 mm to 1 meter
Non-concrete floor finishes (e.g., timber, vinyl, decking): Assessed from 2 meters
Tiled surfaces: Assessed from 2 meters
Concrete or asphalt surfaces: Assessed from 3 meters
Roofing: Assessed from 3 meters
Architectural masonry feature walls: Assessed from 6.1 meters in diffuse lighting
Timber decking: Assessed from 2 meters
Lighting Conditions for Inspection
Painted surfaces should be assessed under non-critical lighting conditions, meaning the light source is diffused and not parallel to the surface. Side lighting or strong direct sunlight can exaggerate surface imperfections that are not typically visible under standard conditions.
Critical lighting occurs when sunlight or artificial lighting is positioned at an angle, highlighting surface imperfections.
Non-critical lighting refers to even, diffused light that provides a realistic assessment of surface quality.
Industry standards state that defects that are only visible under critical lighting should not automatically be classified as poor workmanship.
Inspection of Glass & Powder-Coated Aluminium
In addition to painted surfaces, other building materials follow specific industry standards for quality assessment:
Glass surfaces should be inspected from 2-3 meters away in natural daylight to determine if any imperfections are present.
Powder-coated aluminium finishes are assessed from a minimum of 2 meters away to ensure a uniform appearance, texture, and color, with minor defects being acceptable depending on the location and purpose of the surface.
Surface Defects and Acceptable Standards
Not all minor inconsistencies constitute a defect. Industry standards acknowledge that small variations in texture, color, and reflectivity may occur due to environmental conditions and application methods. However, visible defects that fail to meet standard viewing criteria may be considered unacceptable.
By applying consistent assessment methods, contractors, homeowners, and industry professionals can fairly evaluate the quality of a painted finish while considering practical tolerances.
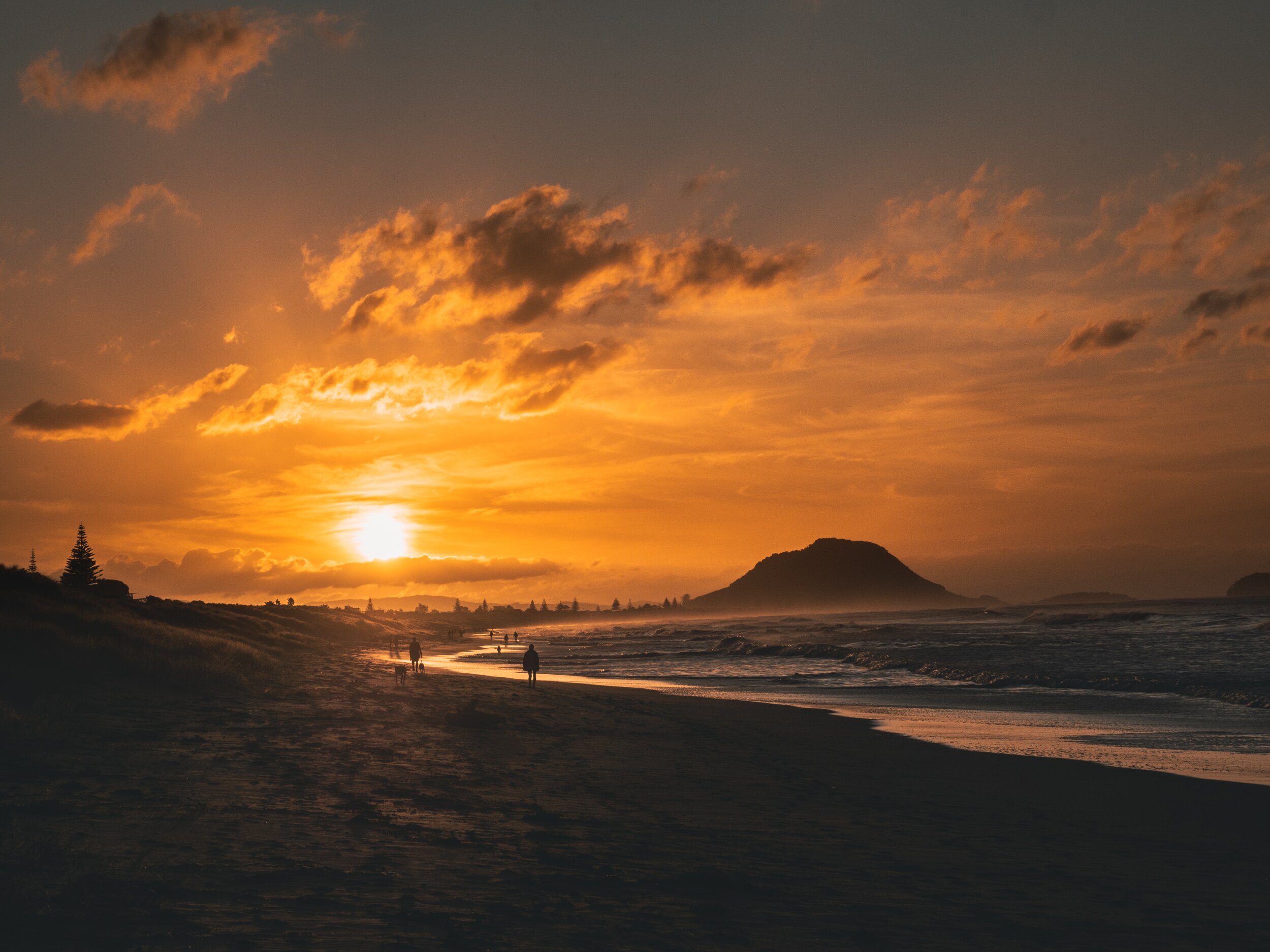